Enhance customer satisfaction by operating a business that offers interconnected mill products
SAP S/4HANA Public Cloud for Mill Industry: Explore how we empower alternative sales approaches and create seamless customer interaction, oversee all profit-focused supply chains, and excel in plant and asset operations, regardless of your industry, such as metal manufacturing, cement production, textile, packaging, or furniture. With SAP S/4HANA Mill industry leaders can open new opportunities for innovation, increase productivity and lead towards huge success.
Mastering the challenges
SAP S/4HANA Public Cloud Mill Industry product firms encounter fresh prospects and hurdles in the midst of digital disruption. Industry leaders leverage market forces to generate and seize novel business chances. Amid significant opportunities and challenges, it becomes crucial to prioritize the correct strategies for successful digitalization.
Digitalization
The SAP S/4HANA Public Cloud Mill Industry solution leverages Advanced digital tools provide unparalleled connectivity, detail, and swiftness in data retrieval, handling, and examination. The Internet of Things, machine learning, and blockchain emerge as feasible choices for revolutionizing business models and processes.
Globalization and right-shoring
With changing global dynamics and previously affordable labor regions gaining prominence, inquiries about production decisions, internationalization strategies, and geographical selection have attained heightened significance.
Disrupted Strategic Models
In the mill industry, existing strategies face risks from fluctuating energy/raw material prices, mass customization demands, complex supply chains, and geopolitical uncertainties.SAP S/4HANA Public Cloud Mill Industry solution offers adaptability in navigating these challenges with confidence.
Value chain of the Milling Sector
Procurement in the milling sector revolves around sourcing raw materials, negotiating contracts with suppliers, ensuring quality control, managing inventory, nurturing supplier relationships, and maintaining compliance and sustainability standards.
By efficiently managing procurement processes, milling companies can reduce costs, minimize risks, and enhance competitiveness within the value chain.
SAP S/4HANA provides effective production planning by analyzing factors like demand forecasting, current inventory levels, and production capacities. The system can create production schedules and allocation of resource planning efficiently. It enables businesses to meet customer demands by minimizing costs and giving maximum efficiency.
During this stage, the raw materials are processed and made into flour or other milling products. SAP S/4HANA can also help you monitor and control the milling process, ensuring it runs smoothly and efficiently. It can also provide real-time visibility into the production floor, allowing for quick adjustments if needed.
The milling process also involves cleaning and conditioning raw grains, milling them to produce flour, bran, and germ, separating and grading the fractions, purifying and refining the flour, blending and mixing, packaging, and distributing the final products. Quality control measures ensure consistency, and waste management strategies minimize by-product generation.
From grain collection to storage, quality management in milling is a non-stop continuous process. Incoming materials are tested, graded, and conditioned to ensure the best milling. Throughout the process, many parameters are monitored and sometimes analyzed in real-time to maintain consistent product characteristics. Finally, proper storage and packaging safeguard the final product's quality. This focus on quality from start to finish minimizes waste, enhances brand reputation, and delivers a high-end quality product that meets customer demands.
Milling has a fine line between having enough and not too much with inventory management. It requires the prediction of customer needs to ensure a steady supply of raw materials without unnecessary storage costs. Different grain grades and types are strategically stored to minimize waste, and inventory levels are controlled closely to trigger timely resupply and prevent issues. This delicate balance keeps production flowing smoothly and ensures the mill has what it needs to meet customer demands. SAP S/4HANA can be a valuable tool in this process, offering real-time data visibility, optimized planning tools, and integrated management across the entire supply chain, helping millers achieve a more efficient and cost-effective inventory strategy.
Milling success lies in turning flour into profit through strategic sales. Understanding customer needs is very crucial, be it a baker requiring high-protein flour or a home cook seeking a specific grain type. Milling companies differentiate their products based on these needs while maintaining competitive pricing to maximize profits. Additionally, efficient order management ensures customer satisfaction and avoids disruptions. SAP S/4HANA empowers this process by offering real-time data on customers, production, and market trends. With this knowledge, sales teams can personalize offerings, optimize fulfilment, and drive sales growth for the milling company.
Efficient transportation and logistics are the most important parts of delivering flour to customers in the milling industry. This includes selecting the most cost-effective method, be it trucks, trains, or containers, depending on distance and volume. Planning optimized routes minimizes travel time and cost, while strategically using located warehouses closer to customers which will ensure faster deliveries. SAP S/4HANA integrates transportation management with other functions, offering features like route optimization, live tracking, and even automated warehouse controls. This empowers millers to achieve a consitent and cost-effective transportation and logistics strategy.
Keeping the milling operation financially sound requires a lot of time and effort on those books. Finance and controlling focus on this by tracking all expenses, from grain purchases to production and delivery. Analyzing profitability across product lines and customers helps identify areas for improvement. Managing cash flow ensures smooth operations by balancing payments and collections. Finally, generating accurate financial reports provides valuable insights into the company's overall health. SAP S/4HANA plays a very important role by offering a detailed financial management system. It manages data collection, automates reporting, and delivers real-time financial insights. This empowers millers to make data-driven decisions, optimize costs, and maintain control over their financial well-being.
In the milling industry, a skilled workforce is the baseline for success. Human Resources Management plays a crucial role in attracting, developing, and retaining top talent. This involves activities like:
- Recruitment and Selection: Finding qualified candidates with the necessary skills and experience to operate and maintain milling equipment, ensure quality control, and manage various business functions.
- Training and Development: Providing ongoing training programs to equip employees with the knowledge and skills they need to perform their jobs effectively and adapt to every day changing technologies.
- Employee Engagement: Maintaining a positive work environment that motivates employees and maximizes turnover. This can involve offering competitive compensation packages, promoting work-life balance, and recognizing employee achievements.
- Safety and Compliance: Ensuring a safe work environment by implementing proper safety protocols, and training employees on safe work practices.
Data is the new diamond in milling, and reporting and analytics help unlock its full value and make it shine. This powerful duo provides insights into every stage of the milling process. Imagine being able to:
- Track Production Performance: Analyze data on milling efficiency, identify areas for improvement, and optimize production processes to maximize output and minimize waste.
- Monitor Inventory Levels: Gain real-time view into raw material and finished product stock levels, allowing for restocking and preventing stockouts or overstocking.
- Analyze Sales Trends: Identify customer buying patterns, and understand product popularity, and offerings based on market demands, ultimately boosting sales and profitability.
- Measure Quality Control: Analyze quality control data throughout the milling process, identify potential issues and ensure consistent product quality that meets customer expectations.
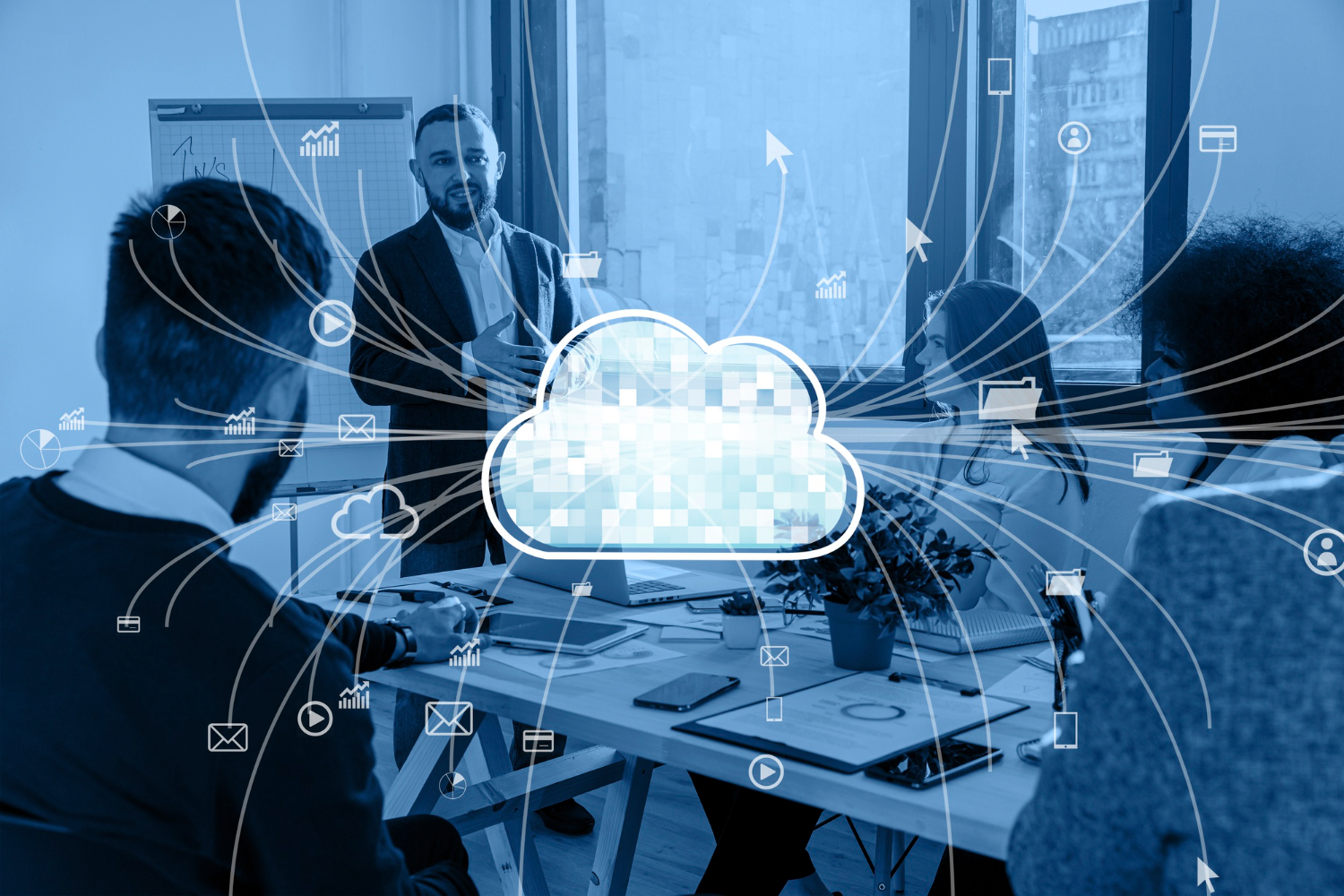
SAP S/4HANA Cloud
Public Edition
Ready-to-run cloud ERP
SAP S/4HANA Cloud, the public edition, ERP solution specially designed for mill products industries. It offers effective functionalities and industry-specific standards to solve the unique challenges faced by mill product manufacturers. By taking advantage of cloud technology, companies in the mill products sector can improve their operational efficiency, optimize processes, and ensure compliance with industry regulations.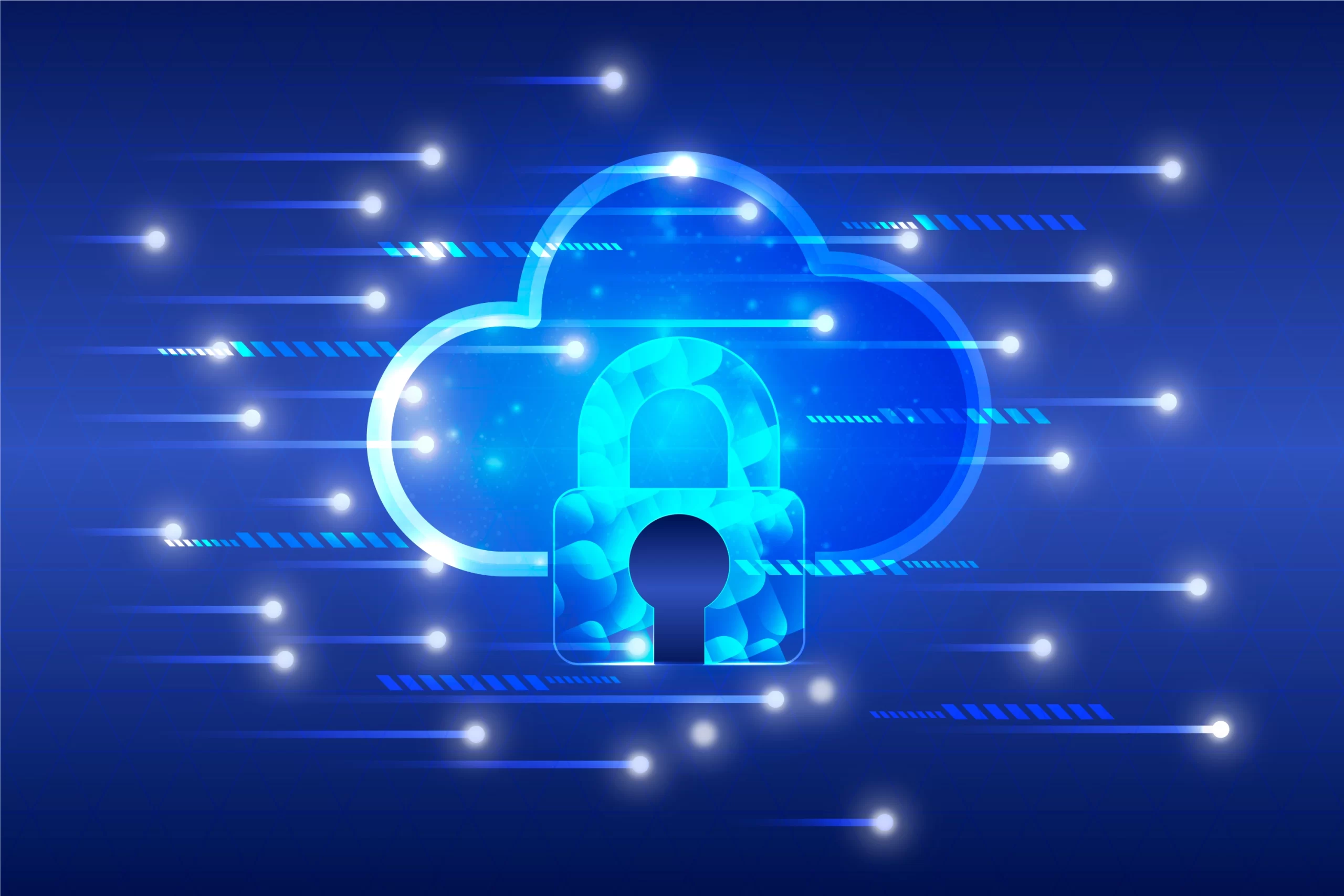